In modern process industries—from chemical plants to oil and gas facilities—control valves play a crucial role as the “final control element” in regulating the flow, pressure, temperature, and level of fluids. Their selection, operation, and integration into process control systems can dramatically affect efficiency, safety, and product quality.
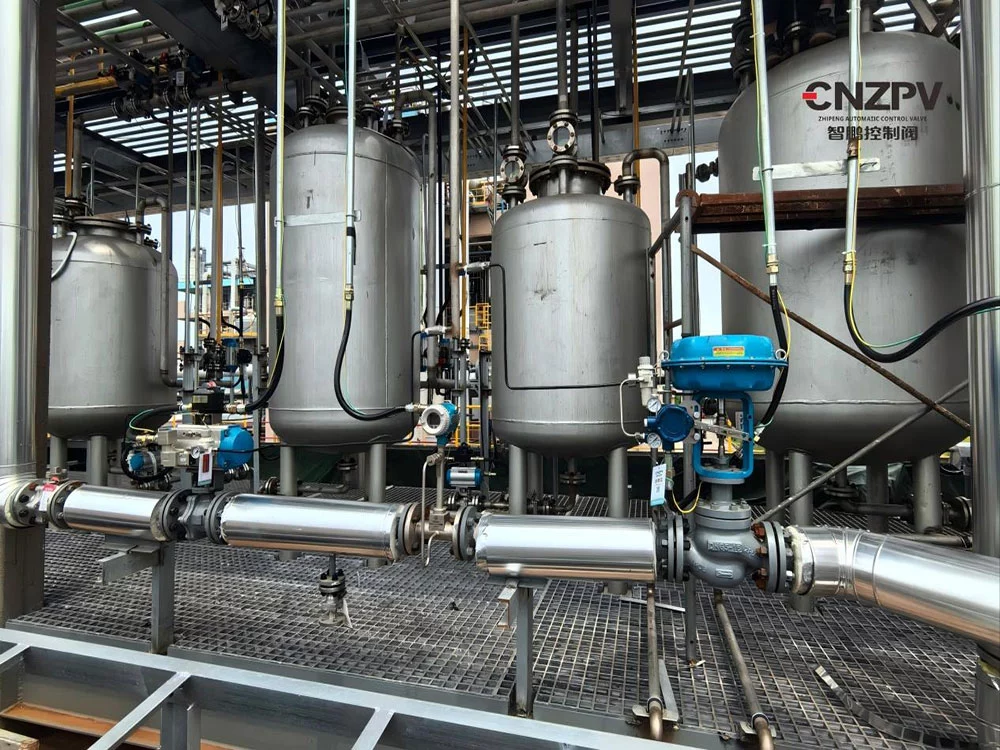
What Is a Control Valve?
A control valve is a power-operated device that varies the flow passage size to modulate the fluid passing through a pipeline. This modulation is based on signals received from a process controller, ensuring that critical parameters such as flow rate and pressure remain within the desired range. In the context of process industries, these valves help stabilize operations and compensate for disturbances in continuous or batch processes.
How Do Control Valves Work?
Control valves work by converting a control signal (often electrical or pneumatic) from a process controller into mechanical motion that modulates the flow of a fluid. Here’s a breakdown of the process:
1. Receiving a Control Signal
A control valve is part of a control loop where sensors measure a process variable (like flow, pressure, temperature, or level). These measurements are sent to a controller, which compares the actual value to a desired set point. Based on the difference, the controller outputs a signal—typically a 4–20 mA electrical signal or a corresponding pneumatic signal—to the valve’s actuator.
2. Actuation and Valve Movement
The actuator (which can be pneumatic, electric, or hydraulic) responds to the control signal by moving the valve’s internal element (such as a ball, disc, or plug). This movement changes the size of the flow passage:
- Linear Valves (e.g., Globe Valves): The valve plug moves up or down to adjust the flow.
- Rotary Valves (e.g., Ball or Butterfly Valves): The valve element rotates (often 90°) to open or close the flow path.
3. Modulating Flow
By varying its position, the valve adjusts the effective area through which the fluid passes. This modulation directly influences the flow rate and pressure in the process line. For example, a partially opened valve will restrict flow, reducing the fluid’s rate, while a fully opened valve will allow maximum flow.
4. Feedback and Positioning
Many control valves incorporate a positioner or feedback mechanism. This system compares the actual valve position (using mechanical or electronic feedback) to the desired position dictated by the control signal. It then fine-tunes the actuator output to ensure that the valve accurately reaches—and maintains—the correct opening. This is vital for processes that require precise control.
5. Integration in the Control Loop
The valve’s modulation of flow helps bring the process variable back to its set point. As the flow or pressure changes due to the valve adjustment, the sensors detect the new conditions and send updated information to the controller. This ongoing loop continuously adjusts the valve to maintain steady process conditions.In summary, a control valve works by:
1.Receiving a control signal from the process controller.
2.Using an actuator to move its internal element.
3.Modulating the flow area to adjust the fluid’s flow rate or pressure.
4.Employing a feedback mechanism to ensure the valve reaches the correct position.
This combination of responsive actuation and feedback makes control valves essential for maintaining process stability and efficiency in industries ranging from oil and gas to water treatment and chemical processing
Types of Control Valves
Control valves are designed in various configurations to suit specific applications. Their design can be broadly classified by the motion of their control element and by the specific flow characteristics they provide.
1. Based on Control Element Motion
- Linear (Sliding-Stem) Valves:
- Globe Valves: With a spherical body and a plug that moves linearly, globe valves offer precise throttling. They are excellent for applications that require gradual flow adjustments and can handle high pressure drops.
- Diaphragm Valves: Using a flexible diaphragm to modulate flow, these valves are ideal for handling corrosive or particulate-laden fluids.
- Rotary Valves (Quarter-Turn Valves):
- Ball Valves: Featuring a spherical ball with a drilled passage, ball valves provide tight shut-off and can be adapted for modulating flow with specialized designs (e.g., V-port or segment ball valves).
- Butterfly Valves: Using a rotating disc, these valves are compact and lightweight. They are particularly cost-effective for large pipe sizes and offer a fast shut-off action.
- Plug Valves: Similar in operation to ball valves but with a cylindrical or tapered plug, they provide excellent sealing and are well-suited for high-temperature and high-pressure environments.
2. Based on Flow Characteristics
- Equal Percentage Valves: The flow increases exponentially with valve opening. They are used in processes where small changes in flow can have a large impact on the process variable.
- Linear Valves: Provide a direct, proportional relationship between valve position and flow rate, useful in applications requiring precise, consistent control.
- Quick Opening Valves: These valves are designed to deliver maximum flow quickly with minimal modulation, making them suitable for on/off applications.
3. Based on Actuation and Special Features
- Pneumatic Control Valves: Widely used in process industries due to their simplicity, reliability, and fast response times. They require a compressed air supply and are often paired with smart positioners.
- Electric Control Valves: Offer high precision and are easy to integrate into digital control systems (e.g., SCADA or DCS). They are generally slower than pneumatic types but provide excellent control accuracy.
- Hydraulic Control Valves: Used in applications where high force is required, hydraulic valves are suitable for high-pressure systems.
Selecting the Right Control Valve
Choosing the optimal control valve involves matching valve characteristics with your process requirements. Consider these factors:
1. Process Conditions
- Fluid Properties: Determine if the fluid is liquid, gas, or slurry. Check for corrosiveness, viscosity, and potential contaminants.
- Temperature & Pressure: High-pressure or high-temperature conditions may require valves with specific materials (e.g., stainless steel, special alloys) or robust designs.
2. Flow Requirements
- Flow Rate and Rangeability: Assess the maximum and minimum flow rates needed. If precise throttling is required, look for valves with linear characteristics (e.g., globe valves).
- Pressure Drop Considerations: Calculate allowable pressure loss. Some valves (like butterfly valves) have lower pressure drops, which might be beneficial in certain applications.
3. Control Characteristics
- Modulation vs. On/Off Control: Decide if your process needs continuous control (modulating valves) or simply isolation (on/off valves).
- Flow Characteristics: Understand if an equal percentage, linear, or quick-opening characteristic best suits your process dynamics.
4. Actuation and Integration
- Actuator Type: Choose between pneumatic, electric, or hydraulic actuators based on response time, available energy sources, and ease of integration with your control system (e.g., SCADA or DCS).
- Feedback and Positioning: Consider valves with smart positioners or integrated feedback systems for enhanced control accuracy.
5. Material and Construction
- Compatibility: Ensure the valve materials are compatible with the process fluid to prevent corrosion, erosion, or contamination.
- Maintenance and Longevity: Evaluate ease of maintenance, sealing performance, and reliability. For example, ball valves with a floating design often offer robust shut-off and long service life.
6. Cost and Life-Cycle Considerations
- Initial and Operating Costs: Balance upfront cost against maintenance, energy consumption, and overall life-cycle costs.
- Application Criticality: For safety-critical applications, investing in a more expensive valve with superior performance may be justified.
Applications in the Process Industry
Control valves are integral components in the process industry—they not only regulate flow and pressure but also ensure that the process conditions remain stable, efficient, and safe. Below is an overview of how these valves are applied across various industries:
A. Chemical Processing
- Precise Reaction Control: In chemical plants, control valves regulate the flow of reactants, helping maintain the exact temperature, pressure, and flow rates needed for optimal reaction conditions.
- Corrosive Fluids Handling: Specially designed valves with corrosion-resistant materials (e.g., lined with PTFE or made of high-grade stainless steel) are used to handle aggressive chemicals.
B. Oil and Gas
- Pipeline Flow Management: In oil and gas pipelines, control valves are used to modulate flow and pressure, ensuring safe transport of crude oil, natural gas, or refined products.
- Safety Shut-Off: Valves such as ball or plug valves can provide reliable on/off control to isolate sections of a pipeline during maintenance or emergency shutdowns.
- Refinery Operations: They help manage the separation and processing stages, controlling steam flow, coolant circulation, and hydrocarbon processing.
C. Water and Wastewater Treatment
- Flow Regulation: Control valves modulate water flow in treatment plants to maintain consistent pressure and flow rates, essential for proper filtration and disinfection.
- Mixing Applications: In water treatment systems, valves may also be used to mix chemicals (e.g., chlorine dosing) precisely with water to ensure effective treatment.
D. Food, Beverage, and Pharmaceuticals
- Sanitary Control: In these industries, valves are constructed from materials that meet hygienic standards and prevent contamination.
- Precise Dosing: They are used to control the flow of ingredients or cleaning chemicals with high accuracy to ensure product quality and safety.
E. Power Generation and HVAC
- Steam and Cooling Systems: In power plants and HVAC systems, control valves regulate steam flow and coolant circulation to maintain optimal operating temperatures and pressures.
- Energy Efficiency: By modulating the flow to match demand, these valves help reduce energy consumption and improve overall system efficiency.
F. Other Applications
- Mixing and Diverting Flows: Three-way control valves are used in processes where mixing of two fluids or diverting flow from one pipeline to another is required.
- Level Control: In tanks and vessels, valves help maintain proper liquid levels by controlling the inflow or outflow based on sensor feedback.
Conclusion
Control valves work as the final control element in a process loop—receiving signals from controllers, adjusting their internal flow path accordingly, and providing continuous feedback to ensure the process variable stays at its set point. Their applications span a wide range of industries where precise control of flow, pressure, temperature, and level is critical for both performance and safety
They are integral to process control, serving as the critical interface between a process controller and the fluid system. With numerous designs—ranging from linear globe valves for precise throttling to rotary ball and butterfly valves for fast on/off operations—engineers can select the optimum valve based on process conditions, fluid properties, and control requirements. By understanding the differences between valve types and the specific needs of an application, industries can improve operational efficiency, maintain safety standards, and ensure the quality of their end products.