Service And Support
Our Service
Our company boasts a worldwide sales and service network, complemented by a dedicated after-sales service department staffed with professional personnel who are committed to providing users with meticulous and thoughtful pre-sales, in-sales, and after-sales services.
Our company pledges the following:
Pre-sales service
We offer users technical consultations, reasonable quotations, as well as warm and attentive on-site inspection services.
In-sales service
We ensure timely product delivery while guaranteeing that no products with quality issues will leave our factory. Additionally, we provide on-site installation guidance,debugging assistance, training sessions tailored to user requirements.
After-sales service:
Adhering strictly to relevant provisions of national industrial product after-sales regulations.Providing 18 months warranty services in strict accordance with the normal operating conditions outlined in the product manual. Offering lifetime technical support for our products.
Import / Export Service
- Packaging Service: We provide safe and reliable packaging for each valve product. Our standard export packing format is Plywood. If customers have special requirements, we will provide corresponding services.
- Logistics/Customs Clearance Services: Our usual export sea-ports are Ningbo or Shanghai, we have reliable international logistics partners to ensure that products can be smoothly cleared in China customs and can quickly and safely arrive at the destination port designated by customers.
- Documents Service: We can provide documents required for destination port customs clearance accordingly to help our customers successfully complete import customs clearance work, Including: Commercial Invoice, Packing List, B/L and C/O, and so on.
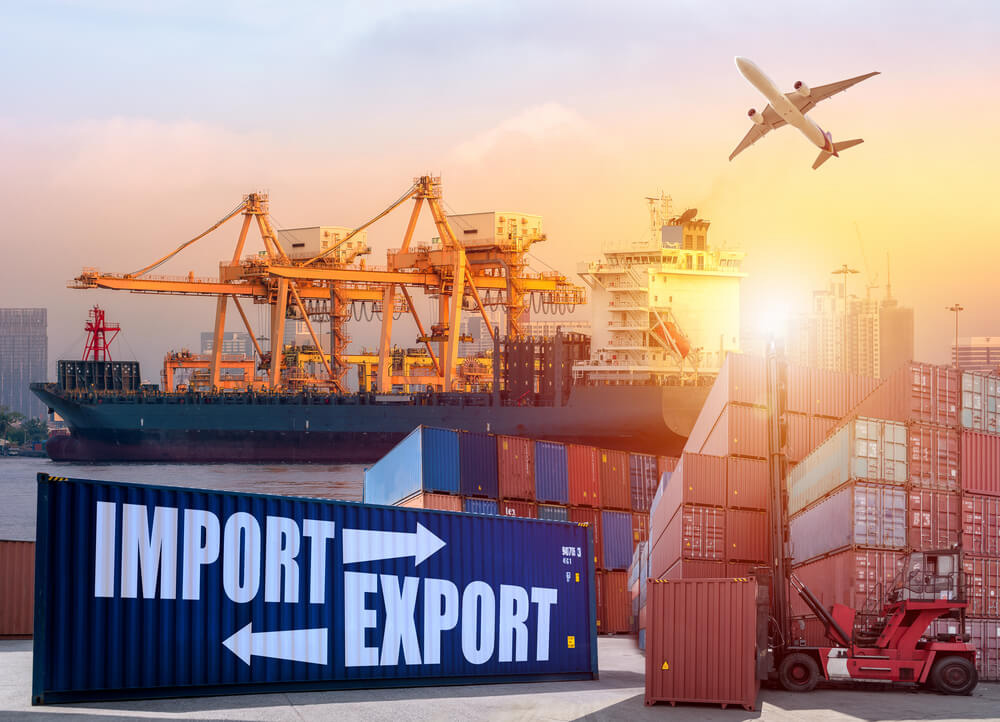
The above represents our unwavering commitment towards exceptional customer care. We wholeheartedly welcome constructive criticism and valuable advice from all esteemed customers as we strive for pleasant cooperation together.
Quality Commitment And Repairs
- 1. The company strictly adheres to relevant national standards such as GB, American standard ANSI, API, British standard BS, German standard DIN, etc., in the design and manufacturing of its various valves.
- 2. We strictly comply with the ISO 9001 quality management system requirements and TS (special equipment manufacturing permit) product requirements for incoming inspection, process inspection, pressure testing, and final inspection. This ensures that any substandard components are prevented from entering the next process and that defective products do not leave the factory.
- 3. Our company is equipped with advanced testing equipment and facilities to ensure that the chemical and mechanical properties of the main valve parts meet national standards
- 4. We have advanced processing equipment and technology (machining, welding, heat treatment, etc.) to guarantee dimensional accuracy, surface roughness, hardness level, mechanical properties,and corrosion resistance of our components meet national standards.
- 5. Strict valve assembly process specifications have been developed to ensure cleanliness of both appearance and inner cavity as well as overall dimensional accuracy during assembly.
- 6. Each valve undergoes rigorous inspection and pressure testing according to industry standards and "Valve Pressure Test Procedure" to achieve a 100% inspection rate before leaving our factory; no defective valves are allowed through.
- 7. Within 18 months after delivery of each valve product,we offer a refund or exchange if there is any failure in sealing or pressure relief due to manufacturing defects.
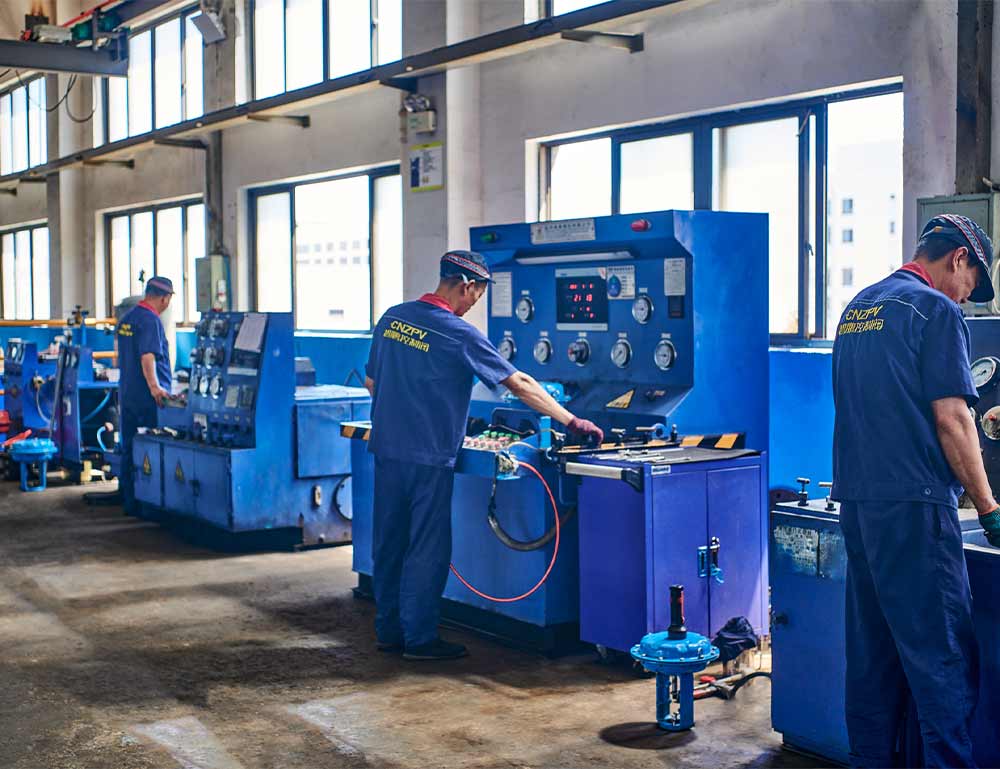
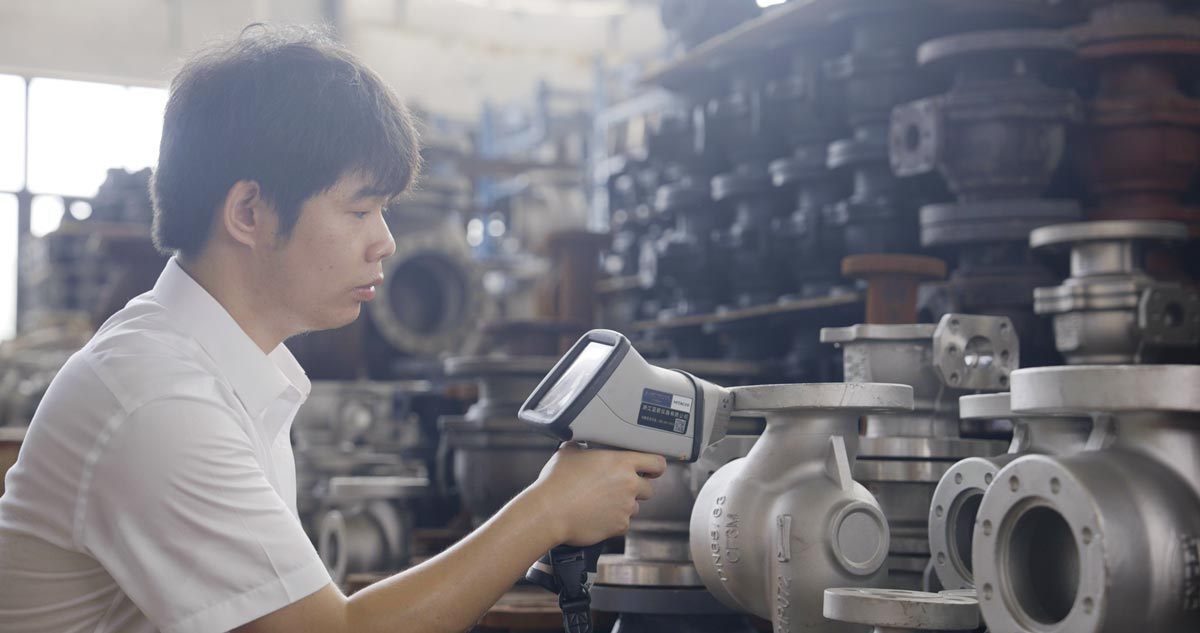
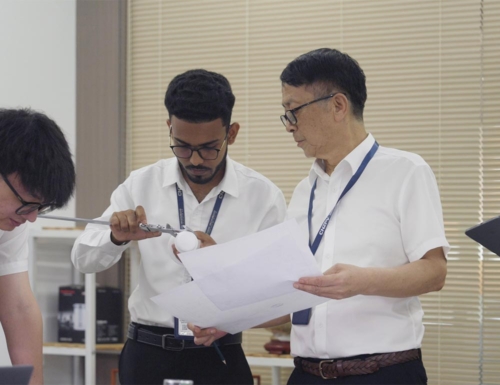
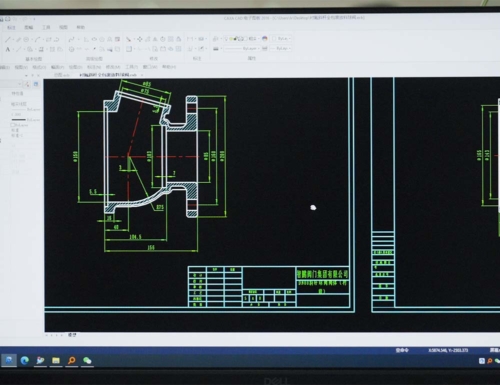
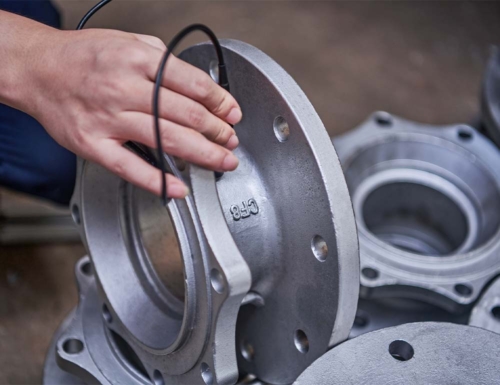

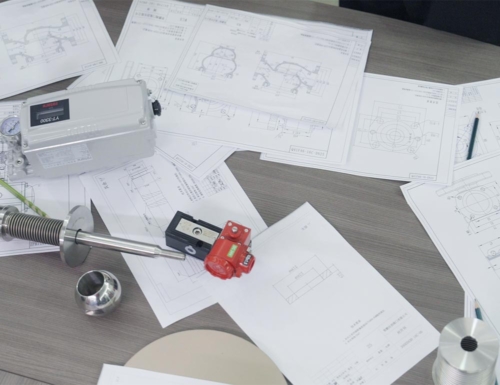
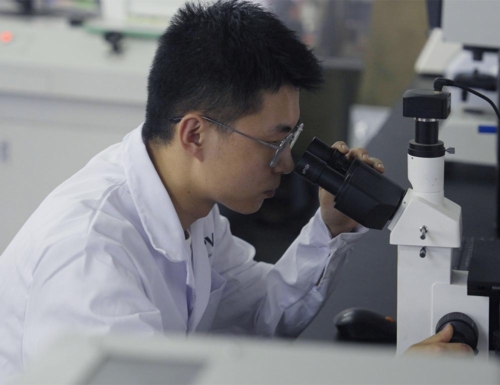
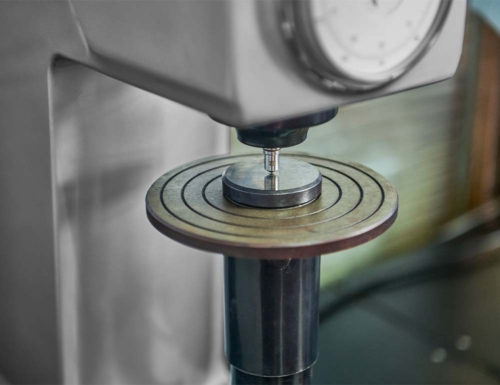
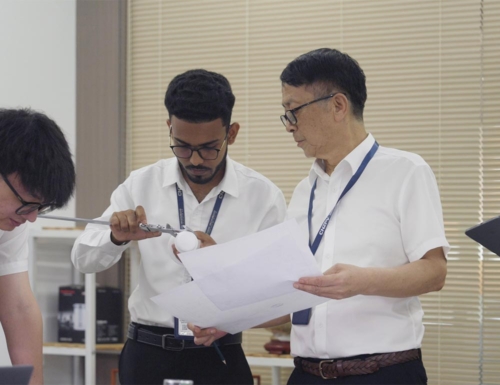
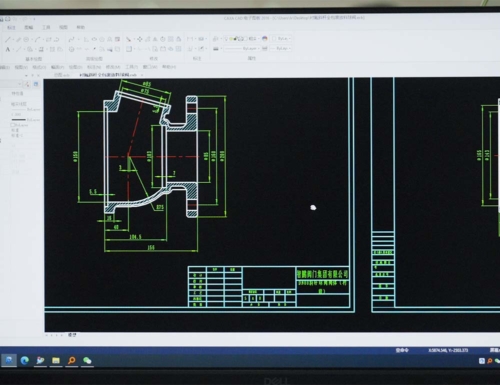
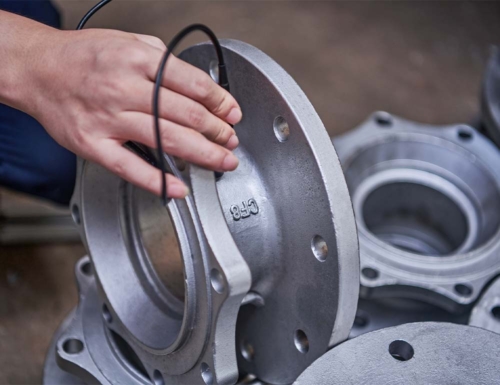

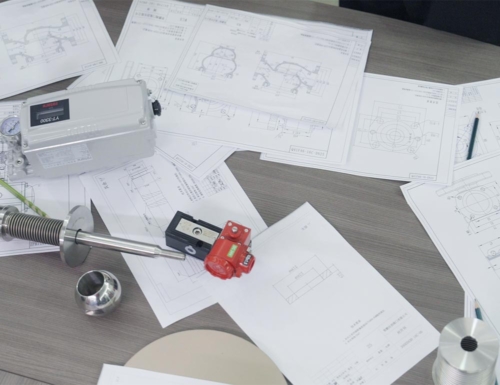
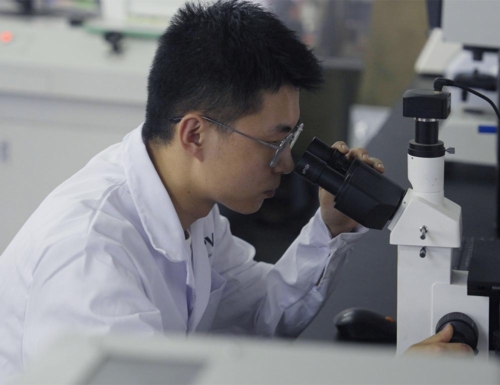