Learn about common issues control valves may have and mitigating techniques.
This article is based on the research conducted by Muhammad Asim Niazi.
Control valves are essential for process control systems and controlling fluid flow. They actuate in response to a signal from the main controller, or programmable logic controller (PLC). The PLC continuously monitors different inputs and is programmed to operate the control valves depending on the process requirement.
Control Valve Types and Applications
Almost all industries use control valves to regulate different process variables, including pressure, flow, level, and temperature. The fluid flow directly impacts these process variables, and control valves can effectively impact these process variables.
Pressure: A valve is programmed to allow the fluid flow until the desired pressure is achieved in systems like steam sterilizers or compressed gas in an air compressor.
Flow: Valves can control infeed water flows or compressed airflow to different pneumatic components in a facility.
Level: Control valves can open or close to change fluid levels in a vessel, such as packaging, where the final product needs accurate filling levels in bottles or glass vials.
Temperature: In some cases, such as a steam autoclave, valves control temperature by allowing or stopping the fluid flow and varying the internal pressure.
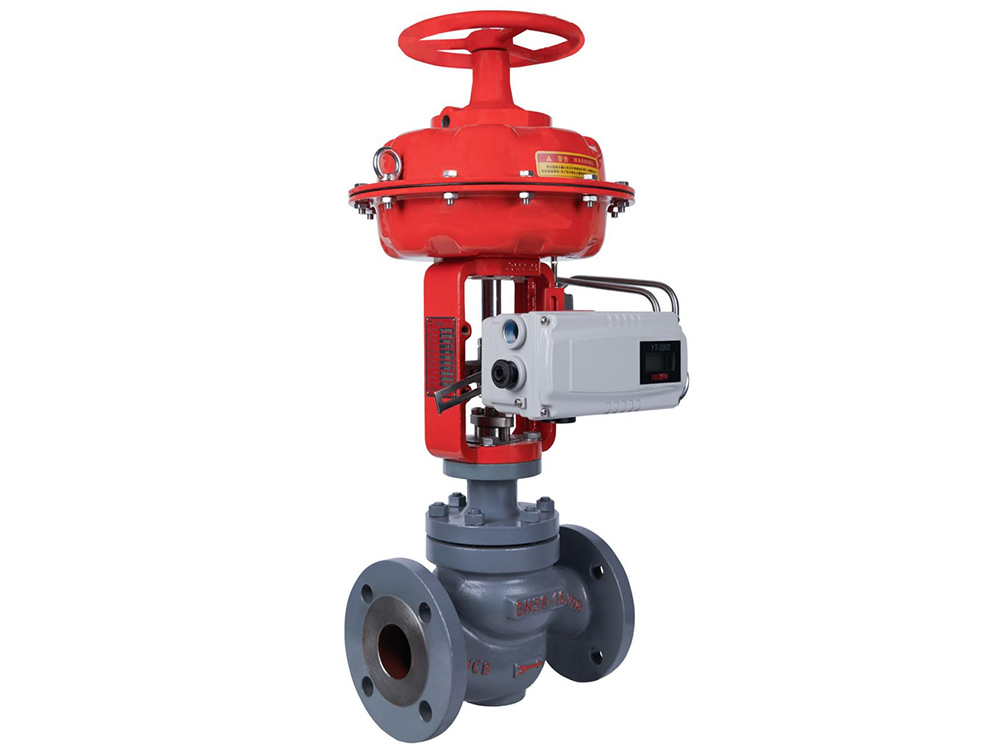
Common Control Valve Issues
Like all process components, control valves are also subject to problems. These problems affect the process. Some common issues with the control valve include size miss-matching, leakage, and improper calibration.
Valve Size Miss-match (Body and Port Size)
Size miss-match means the control valve’s sizing does not correlate with the fluid flow requirements. This happens when the valve is oversized or undersized.
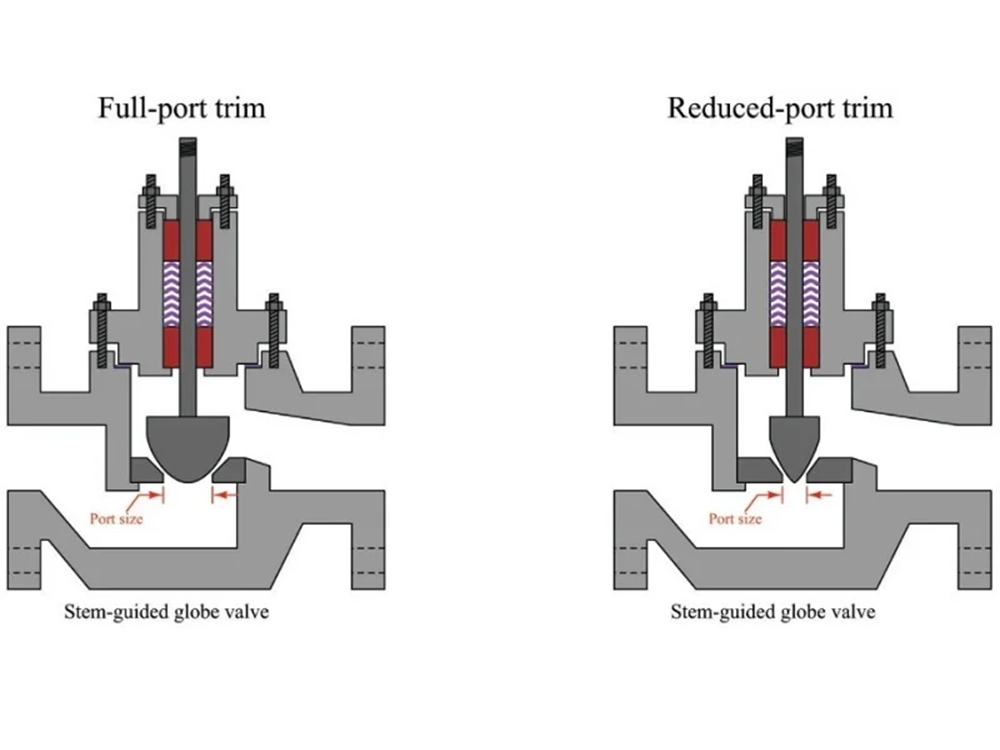
An oversized valve means its rated flow is greater than the process requirement. Oversized valve specifications cause a waste of resources and money. In many cases, although they can deliver the required flow, their output is not steady, and it could deviate from the required flow.
An undersized valve’s rated flow is below the process requirement. When this occurs, a control valve cannot supply the required flow, even if it is entirely opened. Also, when a control valve operates at its maximum capacity, it creates pressure on the valve body, resulting in reduced working life.
Valve Leakage (Internal and External)
Leakage is unwanted fluid flow, resulting in fluid loss. Leaks are often non-controllable and continue to flow until total fluid is wasted or the main fluid supply is completely shut off. The fluid leaks either from the valve’s body or through the output port.
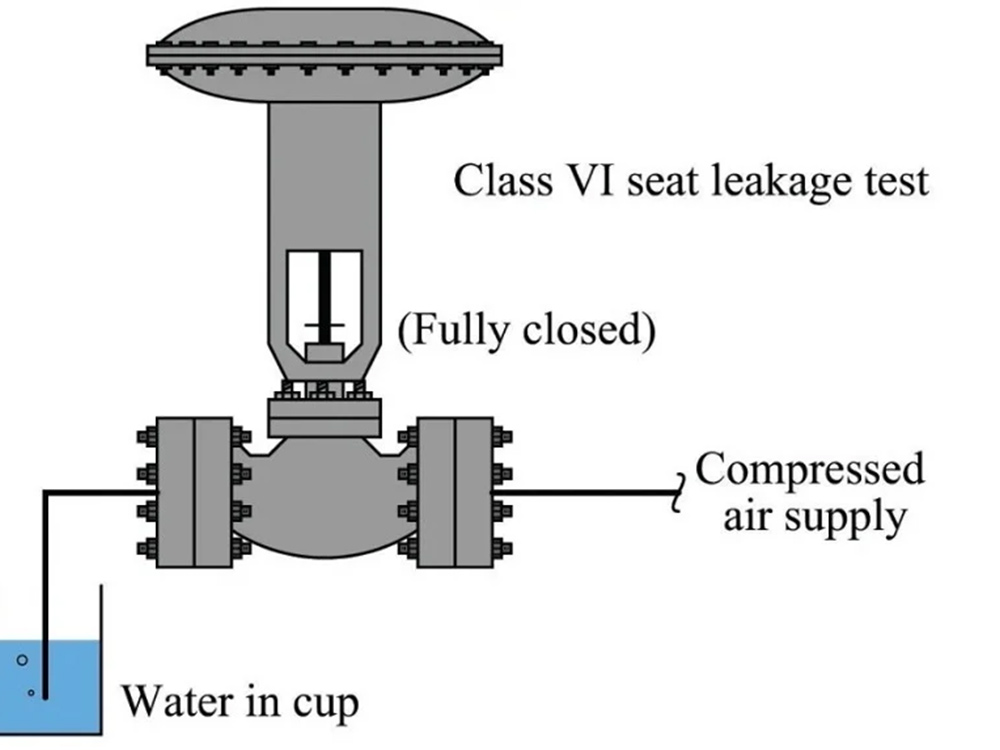
External leakage from the body is due to deterioration in the valve material or improperly sealed and tightened fittings. This condition results in the valve body’s inability to hold the flow (e.g., a crack in the body).
Internal leakage through the valve means it has the command to shut off the fluid flow, but the fluid continues to flow out of the output port. The common reason for this leakage is an internal seat problem, either by age deterioration or contaminants. The interior seat can be stuck or damaged so that the valve cannot respond to the shut-off command.
Seat alignment can be another leakage reason. The seat does not sit properly on the bed of the valve, resulting in fluid flow, even in a close position.
Improper Actuation Element Calibration
The control valve’s actuator is the valve’s controlling mechanism. The actuator receives the commands from the PLC through the current to pressure (I/P) converter.
The I/P converter translates the incoming analog current signal into the equivalent output control pressure. For example, in a common 4-20 mA system, 4 mA from the controller can equal 0 bar, and 20 mA can be comparable to 1.0 bar. The minimum control pressure should shut the valve, and the maximum control pressure should open the valve.
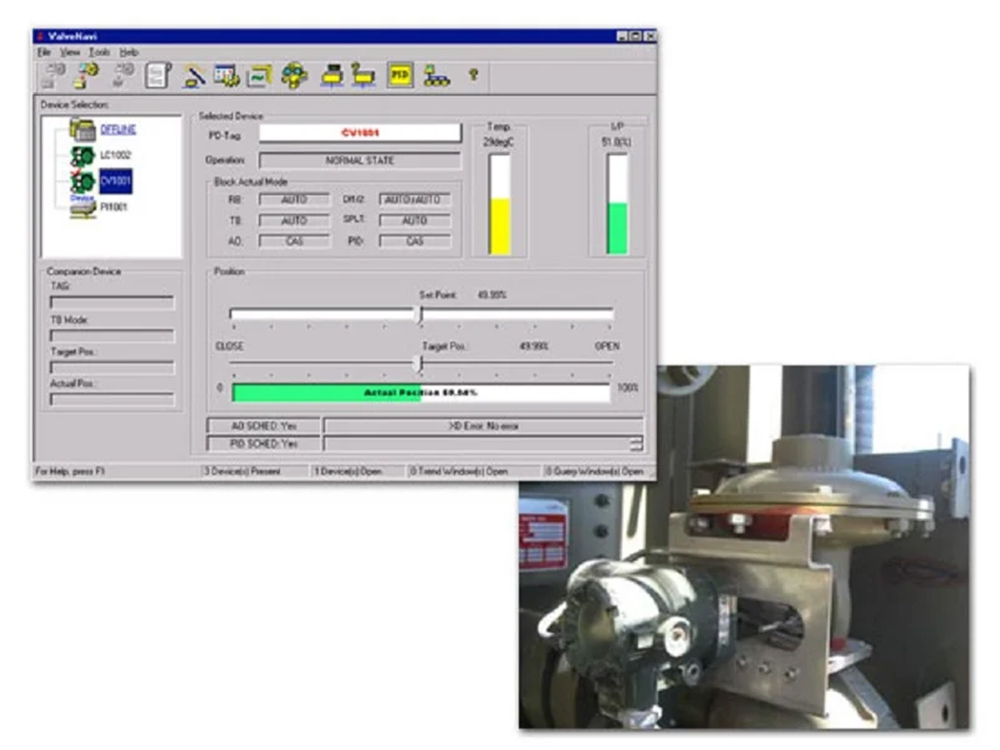
Improper calibration of the actuating element results in improper translation of the incoming signal into the valve position, resulting in incorrect fluid flow characteristics. A signal level from the PLC meant to open the valve halfway could fully open the valve.
Now that we’ve covered common issues, let’s look at potential troubleshooting.
Control Valve Troubleshooting
Keeping control valves in healthy condition extends the valve’s working life and, more importantly, keeps the process safe. Some standard troubleshooting techniques for control valves include preventive maintenance, moisture removal, and calibration.
Preventive Maintenance
Preventive maintenance can prevent potential faults by identifying a problem’s source and eliminating it before it causes trouble.
Some important areas to look at during preventive maintenance for valves include the following.
Visual inspection for degradation and corrosion.
Smooth movement of the mechanical assembly (free from vibration and jerk).
Tightly inserted pneumatic tubing to its connectors.
Pneumatic tubing leakage, bending, or discoloration.
Proper replacement components.
Moisture Removal
It is common for moisture to be contained in compressed air, which may contact the control valve. The moisture penetrates the valve in different components and affects the valve body (i.e., corrosion).
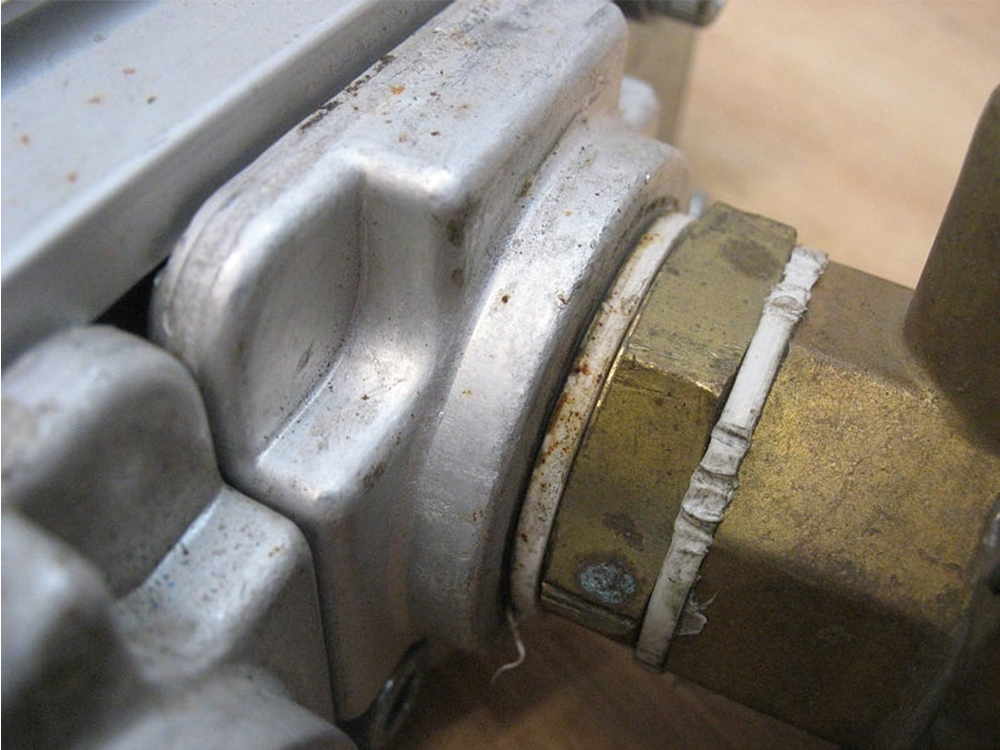
Air systems contain a filter for collecting moisture to prevent adverse effects. These moisture collectors must be discharged frequently to remove the moisture. Otherwise, they can penetrate the valve and cause damage to the valve body.
Positioner Calibration
The positioner valve must be routinely calibrated with the I/P converter output to correctly translate the incoming signal from the PLC. If not calibrated correctly, it can wrongly translate the incoming signal, resulting in incorrect process parameters.
Control valves are widespread within the industry and control all sorts of fluids and gases. As you consider their functions, like any device, they have issues and may need troubleshooting. The above may not be an inclusive list, but as you continue to grow your predictive and preventive maintenance plan, you’ll learn more troubleshooting techniques.
What issues have you had with your control valves? How did you troubleshoot the problem, and what was the result?