With the rapid advancement of the modern chemical industry, the need for valves that can withstand highly corrosive media under special operating conditions has become increasingly critical. Traditional materials like stainless steel and rubber-lined valves often fall short in such environments. While alloys like Hastelloy, Monel, and Alloy No. 20 offer superior corrosion resistance, their high content of rare metals such as Ni, Cr, Ti, Mo, Nb, and Pt makes them expensive and resource-limited.
Modern scientific research has identified fluoropolymers as a game-changing solution. The unique molecular structure of fluoropolymers, characterized by strong fluorocarbon bonds,provides exceptional resistance to corrosion,extreme temperatures, and electrical insulation.These materials can withstand almost all chemical media, including highly aggressive substances like hydrofluoric acid, concentrated sulfuric acid, and even aqua regia.
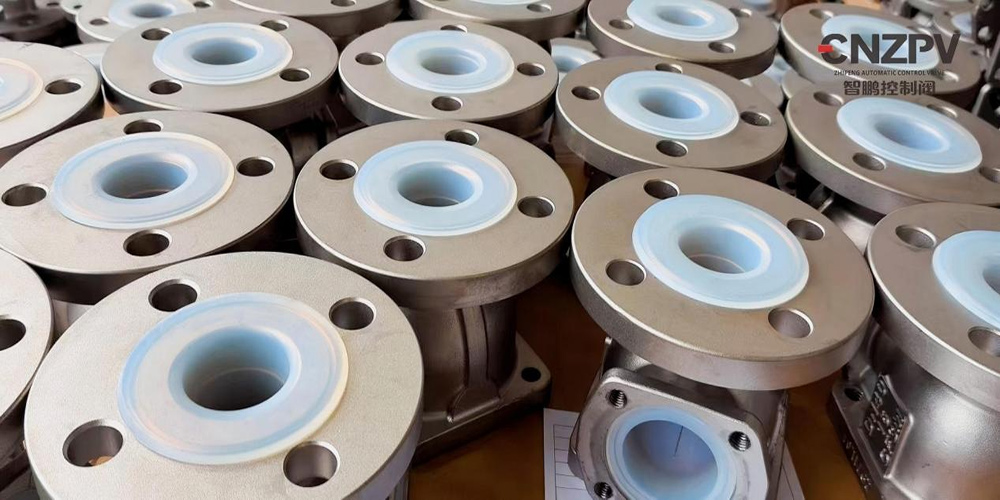
How Fluoropolymer-Lined Valves Work
Fluoropolymer-lined valves are designed by embedding fluoroplastic materials within a standard steel shell.This innovative approach isolates the metal from corrosive media, addressing two key challenges: the low mechanical strength of fluoroplastics and the inability of steel to resist corrosion.By combining the structural integrity of steel with the chemical resistance of fluoropolymers, these valves offer a cost-effective and durable solution for demanding industrial applications.
Applications and Benefits
Fluoropolymer-lined valves,also known as fluoroplastic-lined corrosion-resistant valves, are manufactured by molding or embedding PTFE (polytetrafluoroethylene) or other fluoroplastics like FEP (F46) and PFA into the inner surfaces of valve components.This process is also applicable to pressure vessels and piping systems.These valves are ideal for handling a wide range of corrosive media, including sulfuric acid, hydrochloric acid, hydrofluoric acid, aqua regia, and various organic acids, strong oxidizers, and alkalis.
However,it’s important to note that fluoropolymer-lined valves have a temperature limitation,typically operating between -50°C and 150°C(-58°F to 302°F).They are available in various types, including butterfly valves, ball valves, globe valves, diaphragm valves, gate valves, plug valves, check valves, control valves, and tank discharge valves.
Key Advantages
Superior Corrosion Resistance: Resists all strong acids, bases, and oxidizers.
Temperature Tolerance: Performs reliably in both high and low temperatures.
Electrical Insulation: Excellent insulating properties.
Low Friction and Self-Lubrication: Reduces wear and extends valve lifespan.
Material Considerations
The temperature range and suitability of fluoropolymer-lined valves depend on the combination of metal and non-metal materials used. For example, steel-lined fluoroplastic (WCB + F46) valves can operate between -29°C and 150°C, making them ideal for low-viscosity acidic and alkaline media. However, they are not recommended for use with solid particulate media, as these can damage the lining.
Fluoropolymer-lined valves are essential in modern industries for handling highly corrosive media, offering a cost-effective alternative to expensive alloys like Hastelloy and Monel. These valves combine the structural strength of steel with the exceptional corrosion resistance of fluoropolymers, such as PTFE, FEP, and PFA, making them ideal for applications involving sulfuric acid, hydrochloric acid, hydrofluoric acid, and other aggressive chemicals. With superior temperature tolerance, electrical insulation, and self-lubricating properties, fluoropolymer-lined valves are widely used in industries like chemical processing, pharmaceuticals, and energy.
CNZPV stands out as a leading manufacturer of fluoropolymer-lined control valves in China, renowned for its high-quality, durable, and reliable solutions tailored to demanding industrial environments. Their expertise in combining advanced materials with innovative design ensures optimal performance and longevity, making CNZPV a trusted name in the field of corrosion-resistant valve manufacturing.