Fluorine-lined control valves are widely used in industries such as chemical, petroleum, and pharmaceutical due to their excellent corrosion resistance.However, the high corrosive and pressure of the media pose significant safety risks, particularly the potential for stem blowout. Let us explores the importance of stem blowout prevention design in fluorine-lined control valves and its impact on valve safety and reliability.
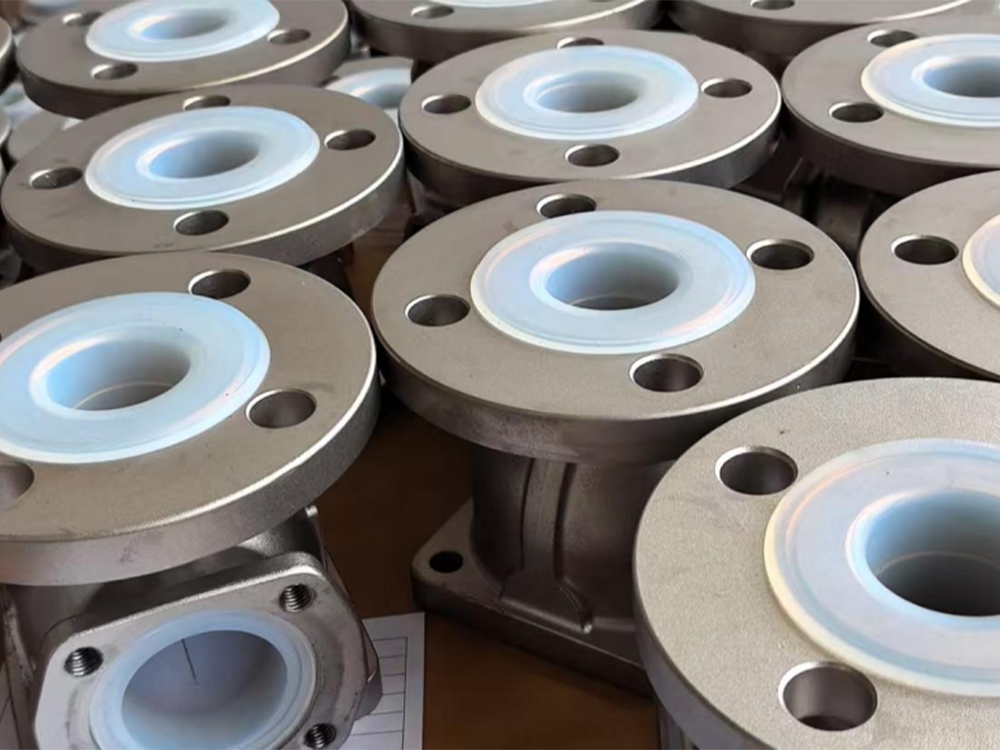
1. Hazards of Stem Blowout
Stem blowout refers to the accidental dislodgement of the valve stem from the valve body under high pressure or abnormal conditions. The hazards include:
Media Leakage: Stem blowout can cause media leakage, leading to environmental pollution, resource waste, and even fire or explosion.
Equipment Damage: The ejected stem may damage the valve or other equipment, resulting in system downtime and economic losses.
Safety Risks: High-pressure media ejection can cause severe injuries to operators.
2. Special Considerations for Fluorine-Lined Control Valves
Fluorine-lined control valves typically use fluorine-based materials (e.g., PTFE or PFA) to resist corrosive media.However, these materials have lower mechanical strength and are prone to deformation or failure under high pressure or temperature fluctuations.Therefore, stem blowout prevention design is particularly critical for fluorine-lined control valves.
3. Key Structural Features of Stem Blowout Prevention Design
Stem Blowout Prevention Step
A step is designed at the connection between the stem and the bonnet to prevent the stem from dislodging under high pressure.
The step dimensions must be precisely calculated based on the valve’s working pressure and media characteristics.
Bonnet-to-Body Connection
Bolted or threaded bonnet connections ensure a tight fit between the stem and the body.
High-strength bolts and sealing gaskets are recommended for high-pressure applications.
Stem Guide Structure
A guide structure between the stem and bonnet reduces radial vibration and deflection.
Fluorine-lined materials can be used for the guide structure to balance corrosion resistance and mechanical strength.
Stuffing box Design
The stuffing box is a critical component for preventing media leakage.It’s design must consider the corrosiveness and pressure of the media.
Multi-layer packing (e.g.,graphite,PTFE) and spring-loaded structures ensure sealing performance and durability.
Stem Limiter
A limiter at the top of the stem prevents excessive movement under abnormal conditions.
Mechanical limiters or electronic sensors can be used for real-time monitoring and alarms.
4. Engineering Practices for Stem Blowout Prevention Design
Material Selection
The stem material must have high strength and corrosion resistance, typically stainless steel (e.g., 316SS) or Hastelloy.
Fluorine-lined materials should have excellent mechanical properties and temperature resistance, with PTFE or PFA being preferred.
Strength Calculation and Simulation Analysis
Finite Element Analysis (FEA) simulates stress distribution under high pressure and temperature fluctuations to optimize stem and bonnet design.
Strength verification according to ASME, API, and other international standards ensures valve safety.
Testing and Validation
High-pressure and fatigue tests are conducted before delivery to validate the reliability of the stem blowout prevention structure.
Field testing or third-party certification is recommended for special operating conditions.
5. Importance of Stem Blowout Prevention(Anti Stem Blowout) Design
Enhanced Safety: Effectively prevents stem blowout, reducing the risk of media leakage and equipment damage.
Extended Service Life: Optimized design and material selection improve valve durability and reliability.
Reduced Maintenance Costs: Minimizes downtime and replacement costs caused by stem blowout.
Compliance with Industry Standards: Meets international standards such as ASME, API, and ISO, enhancing market competitiveness.
6. Conclusion
The stem blowout prevention design is crucial for ensuring the safety and reliability of fluorine-lined control valves. Through rational structural design, material selection, and engineering validation, stem blowout can be effectively prevented, reducing operational risks and extending valve service life. In the future, with the continuous development of industrial technology, stem blowout prevention design will become more intelligent and refined, providing comprehensive safety assurance for fluorine-lined control valve applications.
Why Choose Our Fluorine-Lined Control Valves?
At Zhipeng Valve Group(CNZPV), we specialize in designing and manufacturing high-performance fluorine-lined control valves with advanced stem blowout prevention features. Our valves are engineered to meet the highest safety and reliability standards, ensuring optimal performance in the most demanding applications.Contact us today to learn more about our products and solutions!